Get This Report about Stahl Specialty Company
Get This Report about Stahl Specialty Company
Blog Article
An Unbiased View of Stahl Specialty Company
Table of ContentsExcitement About Stahl Specialty CompanyThe 2-Minute Rule for Stahl Specialty CompanyGet This Report on Stahl Specialty CompanyNot known Details About Stahl Specialty Company Fascination About Stahl Specialty Company
The subtle difference lies in the chemical content. Chemical Comparison of Cast Aluminum Alloys Silicon advertises castability by minimizing the alloy's melting temperature level and improving fluidness throughout spreading. It plays an essential duty in enabling detailed mold and mildews to be filled up accurately. Additionally, silicon adds to the alloy's toughness and wear resistance, making it important in applications where sturdiness is important, such as automotive components and engine elements.It likewise boosts the machinability of the alloy, making it simpler to refine into finished items. In this means, iron adds to the general workability of aluminum alloys. Copper enhances electric conductivity, making it helpful in electrical applications. It likewise improves deterioration resistance and adds to the alloy's overall strength.
Manganese adds to the toughness of aluminum alloys and boosts workability. It is generally utilized in wrought light weight aluminum items like sheets, extrusions, and accounts. The presence of manganese help in the alloy's formability and resistance to cracking throughout construction procedures. Magnesium is a light-weight element that gives strength and impact resistance to light weight aluminum alloys.
It allows the manufacturing of light-weight components with outstanding mechanical homes. Zinc boosts the castability of aluminum alloys and aids control the solidification process throughout spreading. It improves the alloy's toughness and hardness. It is often located in applications where intricate forms and great details are essential, such as decorative spreadings and specific automotive components.
Getting My Stahl Specialty Company To Work
Since aluminum-silicon alloys have great casting buildings, high gas residential properties, straightforward procedures, and excellent deterioration resistance, aluminum-silicon alloys are most generally utilized in the die-casting sector in the house and abroad. At the same time, aluminum-silicon alloys are also relatively very early and widely identified alloys created and used in die-casting. After constant study and improvement, most of the existing international mainstream aluminum-silicon alloys have actually been settled and are nothing even more than A356, A360, A380, ADC12, B390, and A413.
The main thermal conductivity, tensile stamina, yield toughness, and elongation differ. Amongst the above alloys, A356 has the highest possible thermal conductivity, and A380 and ADC12 have the most affordable.
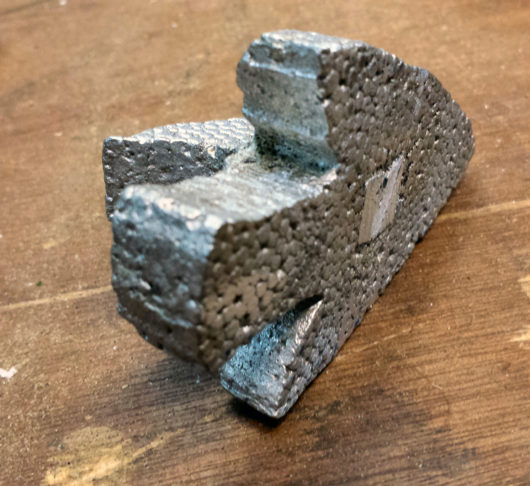
A Biased View of Stahl Specialty Company
In precision casting, 6063 is fit for applications where detailed geometries and premium surface coatings are extremely important. Examples consist of telecommunication enclosures, where the alloy's remarkable formability enables sleek and visually pleasing designs while preserving structural honesty. In the Lighting Solutions sector, precision-cast 6063 parts create elegant and effective lights fixtures that call for intricate shapes and good thermal efficiency.
(https://www.figma.com/design/5dtta9biYAvurKhKjAAp7p/Untitled?node-id=0-1&t=AoovjzyjwBUdKG93-1)
The A360 shows remarkable elongation, making it ideal for complex and thin-walled parts. In accuracy spreading applications, A360 is appropriate for industries such as Customer Electronics, Telecommunication, and Power Tools.
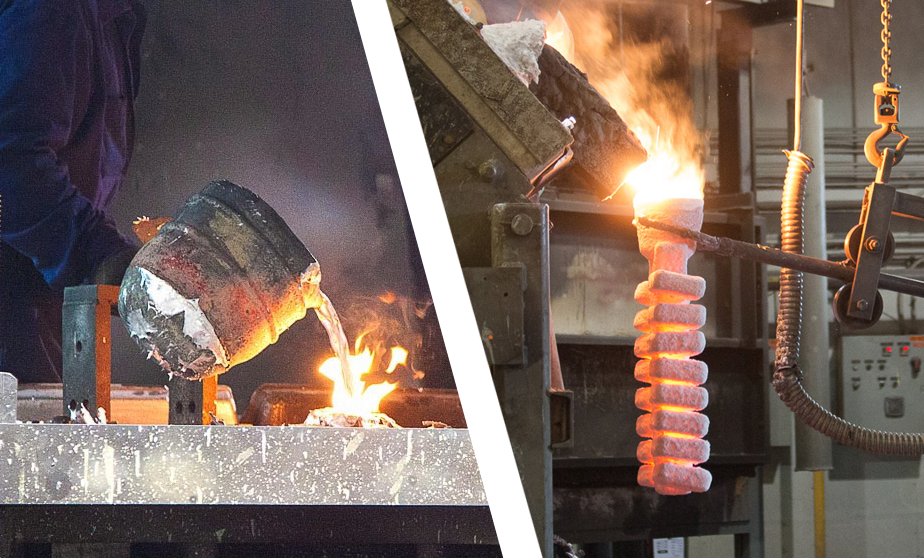
In precision casting, light weight aluminum 413 shines in the Customer Electronics and Power Equipment markets. This alloy's superior deterioration resistance makes it a superb choice for exterior applications, making certain durable, long lasting products in the mentioned industries.
The Best Strategy To Use For Stahl Specialty Company
As soon as you have decided that the aluminum die casting procedure is ideal for your project, an important next action is selecting the most appropriate alloy. The light weight aluminum alloy you select will considerably impact both the spreading procedure and the properties of the last product. Because of this, you must make your choice carefully and take an enlightened technique.
Establishing the most suitable aluminum alloy for your application will suggest considering a broad variety of qualities. The first classification addresses alloy attributes that affect the manufacturing process.
The alloy you choose for die spreading straight influences numerous aspects of the casting process, like exactly how simple the alloy is to function with and if it is vulnerable to casting issues. Warm breaking, also referred to as solidification splitting, is a typical die spreading issue for aluminum alloys that why not try here can cause internal or surface-level tears or splits.
The Ultimate Guide To Stahl Specialty Company
Particular light weight aluminum alloys are much more at risk to warm splitting than others, and your selection should consider this. An additional common defect located in the die spreading of aluminum is die soldering, which is when the actors adheres to the die wall surfaces and makes ejection challenging. It can damage both the cast and the die, so you must seek alloys with high anti-soldering homes.
Deterioration resistance, which is already a notable attribute of aluminum, can vary considerably from alloy to alloy and is an essential characteristic to consider depending upon the environmental problems your product will be exposed to. Use resistance is an additional building commonly sought in light weight aluminum products and can distinguish some alloys.
Report this page